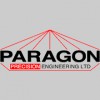
Paragon Precision Engineering was formed in 1995 by engineers John Kent, Steve Voak and Gary Mayes. Starting in one factory unit in Ely we soon expanded into another unit. The company has grown steadily since and in 2001 we had a purpose built factory constructed providing 11,000 sq ft of engineering space.
Paragon is dedicated to implementing world class standards across all functions, and committed to achieving outstanding customer service for all its customers. We are proud to have achieved the LRQA ISO: 9001 certification of quality. The company now employ 34 members of staff, most of whom have been with us for over 15 years.
Paragon is dedicated to implementing world class standards across all functions, and committed to achieving outstanding customer service for all its customers. We are proud to have achieved the LRQA ISO: 9001 certification of quality. The company now employ 34 members of staff, most of whom have been with us for over 15 years.
Services
A complete engineering solution which includes CNC milling and turning, sliding head work, laser marking, engraving, fabrication and welding. At Paragon we pride ourselves on providing a high quality service for all your precision engineering and fabrication requirements. Our highly skilled team are experienced in working with a wide range of materials and to exacting specifications.
With 12 milling machines, Paragon offer a comprehensive machining service with both horizontal and vertical CNC milling centres. CNC machining provides the ideal means of prototyping and producing complex, precisely specified parts, with minimal set-up costs. Paragon's largest machines are the versatile horizontal and vertical machining centres, the Haas HS1 and VF8.
Paragon offer a full conventional milling & lathe setup including vertical boring and full toolroom facilities. Rapid production of high volume runs can be produced on our CNC lathes where tolerances can be as fine as a few microns for maximum precision. Coupled with extensive experience this allows us to complete simple or complex machining requirements using regular or more unusual materials.
Paragon's Sliding Head CNC lathes enable a whole range of very complex parts to be manufactured in one go, to very close tolerances, at a competitive price. The flexibility, capability and capacity of our CNC lathes offers bespoke precision CNC engineering services and the manufacture of high specification components to suit almost all needs.
Paragon benefits from over 20 years' experience in the specialist metal fabrication industry, providing the design and fabrication of metal and alloy products ranging from small precision components to large industrial fabrications. We are ideally placed to cater for a diverse customer base and accommodate the needs of a wide range of industries including Transport, Defence, Construction, Aerospace and Energy.
Reviews (3)
Chas Vin
Sep 16, 2020
Report
Michael Misson
Jun 29, 2020
Report
I have used Paragon many times over the years, after trying 4 other engineering companies I know how to measure them. (2 of which have now closed) As mentioned in another review they don't always get it right first time but they rectify their mistakes. Not all engineering companies will stand by there work, instead blaming drawings or the materials. As they say
"A man who has never made a mistake has never made anything".
"A man who has never made a mistake has never made anything".
Tom Watkins
Dec 09, 2015
Report
I'm a design engineer reviewing based on my recent first time experience dealing with Paragon
We placed a large order for machined plates and PTFE sealing parts. The parts (which arrived 3 weeks late) came in wrong to drawing, badly marked and poorly finished. We have had to send parts back twice to be redone. Tolerances and finishing details stated on drawings seem to be treated as a general guidelines rather than requirements. O ring groves where milled out rather than turned and were so burred they would have sliced and seal in half.
We are now 8 weeks late on what was an original 8 week lead
We placed a large order for machined plates and PTFE sealing parts. The parts (which arrived 3 weeks late) came in wrong to drawing, badly marked and poorly finished. We have had to send parts back twice to be redone. Tolerances and finishing details stated on drawings seem to be treated as a general guidelines rather than requirements. O ring groves where milled out rather than turned and were so burred they would have sliced and seal in half.
We are now 8 weeks late on what was an original 8 week lead