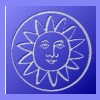
It seems as though the UK Government is determined to turn a crisis into a drama. Despite the success of the vaccination programme and allowing hundreds of thousands of sports fans to attend "test events" the rest of us are left dealing with an out of control NHS App that is pinging large sections of.
During the lockdown we have been working hard in the background to prepare for our customers returning to some sort of normality. We are re-launching our website which we hope users will find more useful and responsive. We have put a great deal of effort into improving the product information presented and updated the information.
During the lockdown we have been working hard in the background to prepare for our customers returning to some sort of normality. We are re-launching our website which we hope users will find more useful and responsive. We have put a great deal of effort into improving the product information presented and updated the information.
Services
The DLS Story
Report
We feel DLS Plastics is the UK's leading manufacturer and supplier of injection molded products - your 'one stop shop' for product design, tool construction and injection molding. Our facilities house full 3D CAD, tool manufacture, injection molding and distribution worldwide.
Whether you're wanting a product from the DLS catalogue or planning your next commercial project, we at DLS know that you may have lots of questions to ask and decisions to make when it comes to fitting the correct component, so why not speak to one of the team who can offer their expert advice.
Whether you're wanting a product from the DLS catalogue or planning your next commercial project, we at DLS know that you may have lots of questions to ask and decisions to make when it comes to fitting the correct component, so why not speak to one of the team who can offer their expert advice.
Product Design
Report
Unlike Stereolithography, Selective Laser Sintering works with powdered materials (not resin), a laser beam fuses powder particles together to reflect 3D data as designed. The key advantage of this type of 3D printing is that parts can be produced in Nylon 12 PA650 or PA615-GS (Glass Filled) - this provides a more true to life representation of a finalised nylon product as well as increased strength.
Tool Manufacturing
Report
After you have taken delivery of your products from us that's not the end, it's just the beginning. At DLS Plastics we are committed to providing you with in depth support from start to finish. We want to build a lifelong working relationship, that's why we provide on-site backup for newly manufactured tools as standard.
Plastic Injection Moulding
Report
Gas assist injection moulding is a process where nitrogen is injected into the melt stream to form a bubble and core out the part, leaving a hollow void in a predetermined position within the moulding. Strength - Tubular structures within the mouldings provide strength and rigidity.
For example our range of gas injected Grab Handles are Pull Tested and able to withstand 125kg of weight hung from them without breaking, despite weighing on average under 150g.Weight Reduction - If your product incorporates large sections of moulding, creating a hollow core in those sections allows for a lower material content; this in turn greatly reduces the final component weight.
For example our range of gas injected Grab Handles are Pull Tested and able to withstand 125kg of weight hung from them without breaking, despite weighing on average under 150g.Weight Reduction - If your product incorporates large sections of moulding, creating a hollow core in those sections allows for a lower material content; this in turn greatly reduces the final component weight.
Product Testing
Report
If the component is expected to withstand a certain amount of weight when in use, we are capable of simulating that and fine tuning a product to be strong enough for your requirements. Originally used to test and prove the strength of our range of leisure vehicle grab handles, we have adopted a test recommended by the National Caravan Council.
Reviews
Be the first to review D L S Plastics.
Write a Review