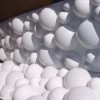
Project Plastics Ltd are specialists in the fabrication of Perspex and acrylic products. We are also experts in plastic fabrication of materials such as Polycarbonate, PETG, PVC, Foam PVC, ABS, HIPS, and Engineering Plastics. Project Plastics was formed in 1994. Our company has been producing bespoke plastic requirements for a range of customers ever since.
We pride ourselves on the fact that we can take large rigid sheets of plastic and then cut, drill, rout, polish, bend, mould, bevel, turn, stick and shape into great designs and displays that our customers have sent from all over the world. Our work has increased by so much that in 2002 Project Plastics moved to a larger factory and then added an extra mezzanine floor to add further production space a year later.
We pride ourselves on the fact that we can take large rigid sheets of plastic and then cut, drill, rout, polish, bend, mould, bevel, turn, stick and shape into great designs and displays that our customers have sent from all over the world. Our work has increased by so much that in 2002 Project Plastics moved to a larger factory and then added an extra mezzanine floor to add further production space a year later.
Services
We have a large 3mt wide x 2mt deep x 2mt high moulding oven in which we can soften plastic ready to form into various sizes and shapes. Movie, Television and Theatre sets, Lighting, Retail, Point of Sale, Window Displays, Exhibitions and Promotions, The Sign Industry, The Gaming Industry, Architectural, Engineering, Marine, Museums and Galleries, Universities, Colleges and Schools, to name a few.
Welcome to Project Plastics the UK's leading bespoke Acrylic point of sale display manufacturing specialist. Project Plastics specialise in bespoke fabrication of acrylic display products for all point of sale requirements. The wide range of products provides for almost any combination, resulting in the simplest yet most effective way to display all types of literature.
Project plastics limited were commissioned by one of their customers to produce an Exciting space age back drop to their exhibition stand. Opal 050 Perspex acrylic was used to produce the dome hemispheres which were then pushed thru special created precision cut and rebated Opal 050 Perspex CNC back boards.
Acrylic and Perspex once heated in our 2 large moulding Ovens to a certain temperature becomes flexible and can be formed into complex shapes. Our largest oven is 3mt x 2mt x 2mt tall added with experience of our fabricators means we are only limited by our customers imagination. We can offer single Curvature thermoforming's or drape forming to produce shapes to your requirements.
At Project Plastics we use the latest vacuum forming technology to create a huge range of plastic display units and bespoke products at very low prices and fast turnaround times. Because of our diversity Project Plastics were chosen to produce The red vac formed ABS stands for the whole UK launch of Virgin Mobile.